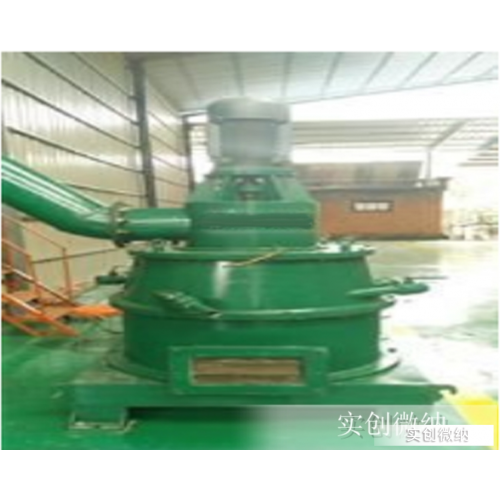
crushing and grading equipment for synthetic graphite
Your message must be between 20 to 2000 characters
Contact NowDetailed Introduction:
I. Working Principle:
After rough crushing, the material is evenly fed into the main crushing chamber through the feeding device. The material collides with the hammer head at a high speed, and achieves ultrafine crushing through mutual impact, collision, friction, shearing, and extrusion between particles. The crushed material is then transported to the impeller grading area by the ascending airflow for forced grading. Under the action of centrifugal force from the grading wheel and the suction force of the fan, the separation of coarse and fine powders is achieved. Qualified fine powder is collected by the cyclone collector, while unqualified powder is returned to the crushing chamber for re-grinding by the internal classifier. The purified gas is discharged by the induced fan.
II. Performance Advantages and Features:
-
High grading accuracy with no large particles, adjustable fineness within the range of 100-1500 mesh.
-
Optimized design of the crushing mainframe and classifier specifically for the adhesive characteristics of graphite/carbon/petroleum coke powder, effectively solving the issue of adhesion, improving production yield, and preventing large particles.
-
Low wear: The crushing hammers and gear rings (liners) are made of superhard alloy material through special processes. Wear-resistant treatment is applied to easily worn parts, greatly improving service life, which is 4-5 times longer than other similar models, and significantly reducing iron impurity pollution.
-
Low installed power, further optimized crushing system structure, significantly reducing energy consumption. The installed power is up to 40-50% more energy-efficient than other mechanical crushers.
-
Increases production yield by 20% compared to ordinary crushing equipment for graphite/carbon/petroleum coke materials.
-
Can disperse sintered agglomerated ultrafine materials, achieving a particle size recovery rate of 99%, with particle shaping function, effectively improving bulk density.
-
High automation level, strong stability, and easy operation.
-
The entire machine adopts fully enclosed negative pressure production, with no dust pollution and excellent environmental conditions.
-
Strong mechanical stability, unique flow field design, and constant gas-solid concentration control, ensuring stable operation of the system over time.
III. Technical Parameters:
Equipment Model | Installed Power (KW) | Feed Particle Size (mm) | Output Particle Size (μm) | Output (kg/h) | Remarks |
---|---|---|---|---|---|
SCWN-C400 | ≤65 | ≤10 | 5-150 | 80-1500 | Particle size adjustable |
SCWN-C600 | ≤97 | ≤20 | 5-150 | 200-3000 | Particle size adjustable |
SCWN-C1200 | ≤217 | ≤20 | 5-150 | 400-5000 | Particle size adjustable |
IV. Application Fields:
Widely used in industries such as graphite, carbon, and petroleum coke.
Related Keywords