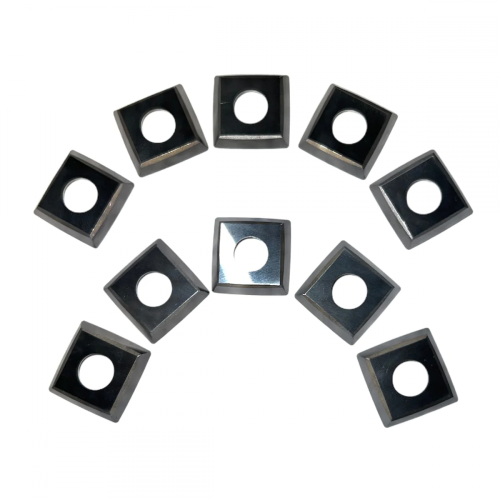
Carbide Insert Knives Used For Wood Planing
-
$0.80100-499 Piece/Pieces
-
$0.78500-999 Piece/Pieces
-
$0.751000-1499 Piece/Pieces
-
$0.73≥1500 Piece/Pieces
- Transportation:
- Ocean, Land, Air, Express, Others
- Port:
- Ningbo, Shanghai, Yiwu
Quantity:
Your message must be between 20 to 2000 characters
Contact NowBasic Info
Basic Info
Place of Origin: | Mianyang |
---|---|
Supply Ability: | 10000pcs |
Payment Type: | T/T |
Incoterm: | FOB,EXW |
Transportation: | Ocean,Land,Air,Express,Others |
Port: | Ningbo,Shanghai,Yiwu |
Product Description
Product Description
Carbide blade is a commonly used tool for metal processing and cutting, which has advantages such as high hardness, wear resistance, and heat resistance. The production process mainly includes the following steps:
1. Material preparation: Choose high-quality hard alloy materials as the substrate for the blade, usually tungsten cobalt alloy or tungsten titanium carbon alloy.
2. Powder metallurgy: Mix alloy material powder with an appropriate amount of binder evenly, then press and shape it, and sinter it at high temperature to combine the powder particles into a sturdy blade.
3. Precision machining: The sintered blade needs to undergo precision machining, including cutting, grinding, polishing and other processes, to ensure the precise size and smooth surface of the blade.
4. Coating treatment: Some hard alloy blades also require surface coating treatment, such as TiN, TiCN, etc., to improve the wear resistance and cutting performance of the blades.
The advantages of discarding hard alloy blades include:
1. High hardness: Hard alloy blades have extremely high hardness and can maintain stable cutting performance during high-speed cutting.
2. Wear resistance: The hard alloy blade has excellent wear resistance, which can maintain a sharp cutting edge for a long time and extend the service life of the tool.
3. Heat resistance: Hard alloy blades have good heat resistance and can maintain stable cutting performance in high-temperature environments.
4. High precision: Hard alloy blades are precision machined and produced with precise dimensions, which can meet high-precision machining requirements.
1. Material preparation: Choose high-quality hard alloy materials as the substrate for the blade, usually tungsten cobalt alloy or tungsten titanium carbon alloy.
2. Powder metallurgy: Mix alloy material powder with an appropriate amount of binder evenly, then press and shape it, and sinter it at high temperature to combine the powder particles into a sturdy blade.
3. Precision machining: The sintered blade needs to undergo precision machining, including cutting, grinding, polishing and other processes, to ensure the precise size and smooth surface of the blade.
4. Coating treatment: Some hard alloy blades also require surface coating treatment, such as TiN, TiCN, etc., to improve the wear resistance and cutting performance of the blades.
The advantages of discarding hard alloy blades include:
1. High hardness: Hard alloy blades have extremely high hardness and can maintain stable cutting performance during high-speed cutting.
2. Wear resistance: The hard alloy blade has excellent wear resistance, which can maintain a sharp cutting edge for a long time and extend the service life of the tool.
3. Heat resistance: Hard alloy blades have good heat resistance and can maintain stable cutting performance in high-temperature environments.
4. High precision: Hard alloy blades are precision machined and produced with precise dimensions, which can meet high-precision machining requirements.
5. Abandoned design: The discarded hard alloy blade adopts a disposable design, avoiding the trouble of re grinding the tool and improving production efficiency and processing quality.
Related Keywords
Related Keywords